16 October 2023
RAAC BRIEFING
Architecture, Building Consultancy, Health & Safety, Industry News, SHW News
Reinforced Autoclaved Aerated Concrete (RAAC) has recently become headline news due to the Government asking some schools to close, or partially close, due to new concerns about structural safety. However, issues with RAAC have been known about for some time.
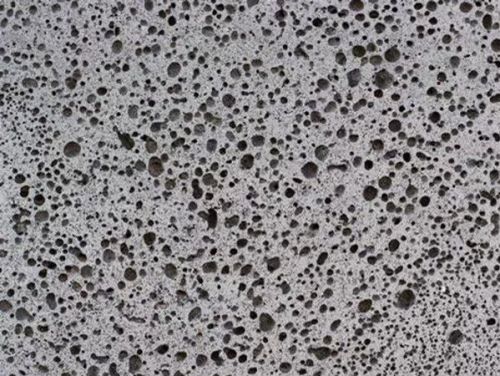
What is RAAC?
Autoclaved Aerated Concrete (AAC) was first developed in Sweden in the 1920s and was then introduced into the UK in the late 1950s. AAC has often been used in the construction of lightweight thermal blocks for buildings.
AAC was then developed into prefabricated planks, which contained reinforcement to improve tensile strength. This was known as Reinforced Autoclaved Aerated Concrete (RAAC). The planks were often used as roof decks, but also used in the construction of floors, internal partitions and vertical wall cladding.
RAAC is typically found in public buildings that were built or modified between the 1950s and the 1990s. However, it may be present in other buildings built or modified during this time.
Manufacture
AAC is not strictly concrete. It does not contain a course aggregate, and it is much lighter and softer than normal concrete. It can be easily cut or chiselled by hand tools.
The raw materials of AAC are typically cement, silica, water and aluminium powder. After mixing, the slurry is cast into a mould. A chemical reaction caused by the aluminium creates small bubbles, which results in a closed cell, cellular concrete mixture. The product is then removed from the mould, cut and cured under high temperature and pressure in an autoclave.
The finished material is usually light grey in colour and can be easily broken or damaged with small hand tools. In cross-section, the cellular nature of the product is easily seen.
Because AAC can be crushed easily and does not bond successfully to steel, the reinforcement needs to be bent into hooks or contain welded cross bars to lock it into place. Also, aerated concrete does not provide the same level of corrosion protection to the steel reinforcement as standard concrete so additional corrosion protection, such as a bitumen coating, is necessary.
Features
RAAC planks are rectangular in section with chamfered edges. Planks are typically 600mm wide, but can vary in width from 300–750mm. The length of planks is typically 2400mm-3000mm, but spans of up to 6000mm are not unknown. The planks are typically 100mm–250mm thick.
RAAC is much more elastic than normal concrete, with deflection of the planks being approximately ten times greater that of an equivalent concrete plank under similar loadings.
Concerns with RAAC
UK production ended in 1982, but it continued to be imported until the mid-1990s. In 1995 concerns were first raised over the durability of the planks used for school roofs, when cracks were discovered. Investigations in 1996 by the Building Research Establishment (BRE) lead them to conclude that the life expectancy of RAAC was approximately 30 years. The use of RAAC in the UK then effectively came to an end.
In February 1999 the Standing Committee on Structural Safety advised owners of both school and non-school buildings with pre-1980 RAAC plank roofs to arrange for them to be inspected if this had not been done since 1994, and recommendations have been given for the regular inspection of RAAC roof planks, particularly those erected prior to 1980.
In 2018 a RAAC plank failed at a school in Essex, which prompted the Government to start monitoring schools with RAAC. In 2019 the Standing Committee on Structural Safety (SCOSS) warned that RAAC planks installed pre-1980 were now beyond their service life, and advised schools that they should be replaced. In the summer of 2023, three incidents lead the Government to ask affected schools to close in part or in full due to safety concerns.
How can SHW help?
If you or one of your clients are concerned that RAAC may be present in a property, please contact one of our team of Building Surveyors who will be able to offer further advice, arrange appropriate inspections, and advise on the necessary remedial measures.